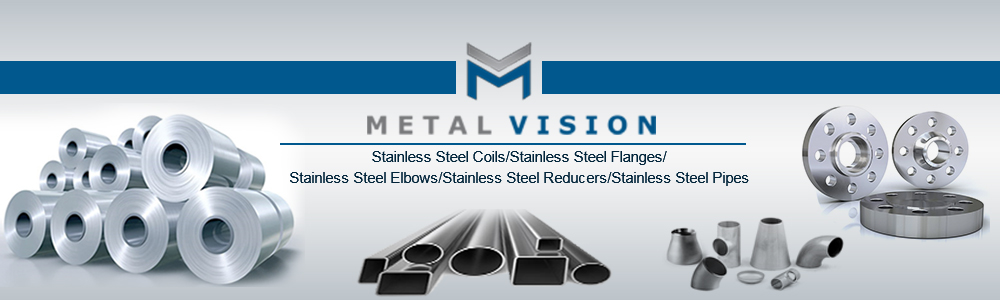
METAL VISION - | E-Showroom
METAL VISION - | E-Showroom
Hot-dip coated with an aluminum/silicon alloy containing 5% to 11% silicon to promote better adherence. It is intended principally for heat resisting applications and also for uses where corrosion resistance and heat are involved. Possible end users are mufflers, furnaces, ovens, ranges, heaters, water heaters, fireplaces, and baking pans.
Coating Method:
Hot Dipping continuous coating method is used for production of the product, in which base metal is dipped in a Pot In this case of 88 to 91 % Aluminum to 5 to 11 % Silicon. In this method both sides are coated simultaneously.
This process assures a tight metallurgical bond between the steel sheet and its aluminium coating, producing a material with a unique combination of properties possessed neither by steel nor by aluminium alone.
Product Features:
Corrosion Resistance Aluminized Steel Type 1 has superior performance compared to zinc coated materials for resistance to atmospheric and salt spray corrosion. Formability Aluminized Steel Type 1 can be used to produce parts containing simple bends to parts with deep drawing requirements. Heat Reflectivity Aluminized Steel Type 1 has excellent heat reflectivity during exposures to temperatures below 800 °F (427 °C), reflecting up to 80% of the radiant heat that impinges upon it.
High Temperature Properties Aluminized Steel Type 1 is an excellent heat resistant material effective up to 1250 °F (677 °C). ALUMI-THERM® is a product designed to provide enhanced high temperature strength at temperatures approaching 1400 °F (760 °C).
Paintability:
For best results, Aluminized Steel Type 1 should be cleaned with a mild alkaline cleaner to remove dirt and oil, followed by phosphate with a zinc phosphate. Chromium and aluminum oxides also give good results as a pretreatment on coil coating lines. Mild abrasion prior to pre-treating may also be used to enhance mechanical bonding of the paint.
Weldability:
A variety of welding processes can be used to join Aluminized Steel Type 1, provided that welding procedures are adapted to the special properties of the material. Resistance spot and projection welding processes are especially suited for Aluminized Steel. High frequency resistance welding and various arc welding processes are also compatible with Aluminized Steel.
Heat Resistance:
The heat resistance of ACMS is excellent compared to that of zinc-coated steel sheet, galvanized steel sheet, and cold-rolled steel sheet. Absolutely no changes in appearance and discoloration are observed even under extended exposure to the temperature of 450.At temperatures higher than 450the coating material transforms to aluminium-iron alloy layer so that heat resistance and corrosion resistance are preserved even if discoloration occurs. The coating maintains its sacrificial properties up to the temperature of approximately 600.
Heat Reflectivity:
Aluminized Coated Steel provided with excellent thermal reflectivity due to the fineness of its surface. The thermal reflectivity of Aluminized Coated Steel at 450??? reaches up to approximately 80%, and this is applied to thermal reflectors for toasters, gas ranges, oil stove, and so forth.
Application | Construction |
Material |